动力电池标准化制造正当时
作者:曹武佳 发布于:2017-05-23 08:32:38 来源:电池中国网
动力电池标准化制造问题已经不是第一次被业内人士广泛提及了,但笔者认为目前再谈这一问题确是最合适不过的。2017年5月,笔者已走访了6家动力电池企业和6家新能源汽车企业,标准化制造问题再次成为热议。
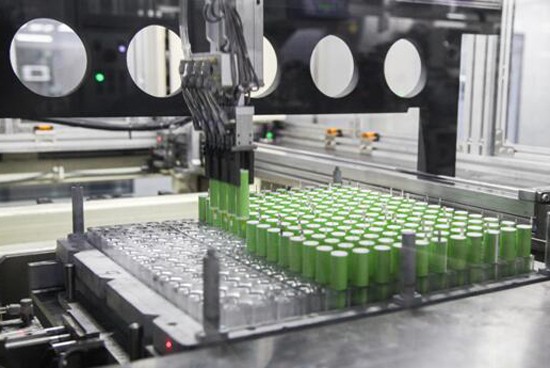
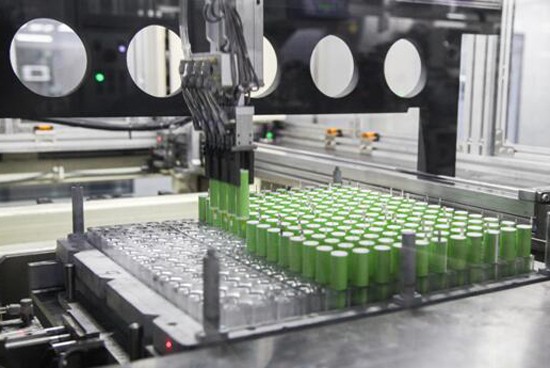
动力电池标准化,动力电池制造
动力电池标准化制造正当时
对于动力电池企业而言,2017年是关键年、突围年、洗牌年,甚至是决胜年,挑战和机遇并存。一方面,“上挤下压”,动力电池企业降成本和提升能量密度的压力倍增,叫苦连天;另一方面,“一带一路”国家战略开启了中国动力电池企业海外布局的大市场。此外,国内新能源汽车产业的快速崛起,以及储能、梯次利用等细分领域的不断发掘、成长,未来市场不容小觑。
在当前行业大背景之下,动力电池标准化制造正当时。调研组了解到,中航锂电在新建产线的时候就考虑到了模块标准化等要求;河南锂动在其第三代产品设计中结合了VDA的标准模块尺寸;多氟多新能源也认为,动力电池降成本和提高安全性的首要前提是标准化。中航锂电副总经理肖亚洲介绍说,“我们现在合作的这几个整车企业,已经提出了明确的规格要求,就是按VDA去做,所以我们现在对乘用车、客车已经做到了模块标准化。”
不单单是动力电池企业开始重视标准化制造问题,国内很多车企也纷纷探索产业发展的模式创新,以降低动力电池的使用成本。长城汽车副总工程师马忠龙认为,随着新能源汽车车型和结构的稳定,标准电芯、标准模组将逐步降低整车的制造成本。此外,宇通客车、海马汽车、东风特专等车企也都非常关注动力电池的标准化制造。
统一标准的道路是曲折的
标准引领行业发展。比如,同样规格尺寸的电池更容易通过各项性能的检测一较高下,这就驱使动力电池生产企业更加重视生产工艺和材料的研究,并有利于整个电池产业的稳健发展。然而,有不少业内人士表示,我国动力电池缺乏通用性,在标准化、规模化生产上的进程依然缓慢,这不仅增加了电池生产成本,也阻碍了动力电池梯次利用、回收等领域的可持续发展。
究其原因,主要因为以下几点:
首先,国内动力电池和新能源汽车产业尚未成熟,各家对于标准的理解都不一样,很难统一;其次,由于动力电池产业处于初级阶段,各家企业尚在探索之中,行业内缺少可以引导标准化形成的一流企业。另外,出于保密的考虑,多数企业不愿将自己制造的动力电池参数公之于众,这使得制定行业标准失去了必要的技术参数作为参考。
变革从这里开始
推进动力电池标准化制造宜早不宜晚,所幸国内多数业内人士已经认识到了它的重要性,并提出了很多宝贵的建议。
全国人大代表、中船重工风帆有限责任公司董事长、党委书记刘宝生代表曾在公开场合建议,在电池型号和模组尺寸、功能和接口上推行标准化,将有效促进大规模生产,带来更加便捷的维修与替换,同时也将带动设备和生产线的标准化,促进电动汽车产业规范、健康发展。
海马电动汽车营销部副部长郑广炜认为,“我们发现电芯的结构各家很难统一,因为每家电池企业的电芯结构都不一样,而模组的标准化相对要成熟一点。”有业内人士进一步建议,应首先把动力电池模组做成标准化,包括尺寸标准化和DR平台标准化,待模组标准化后再反向规定电芯的规格。
电池中国网认为,动力电池的发展是一个动态变化的过程,而标准化制造无疑将为产业发展带来一场变革。短期内,我们应该充分讨论,并主动引导,让市场去选择采用哪种规格的动力电池。而从长远来看,制定合理的模块、规格、序列等标准,形成规模化生产,减少研发与生产成本才是国内动力电池保持竞争力的关键。而且,动力电池标准化应该借鉴国外的成熟经验,充分发挥动力电池相关协会“沟通和发声”的平台作用,从“产学研用”等多个角度,共同推动国内动力电池标准化制造的快速实施。
本网拥有此文版权,若需转载或复制,请注明来源于政府采购信息网,标注作者,并保持文章的完整性。否则,将追究法律责任。
网友评论